Cold Forming
Cold Forming : Introduction
Cold forming is a manufacturing process that plastically deforms metal using dies. It allows for high speed production, little to no material waste compared to conventional machining, and creates a stronger end product due to work hardening of the material.
Basics of Cold Forming
*Header Machine (2-die, 3-blow)
-
STEP.01
Material Cut-off
-
STEP.02
Forward Extrusion
-
STEP.03
Upset1
-
STEP.04
Upset2
-
STEP.05
Backward Extrusion
-
STEP.06
Processing Complete
1. Material Cut-off
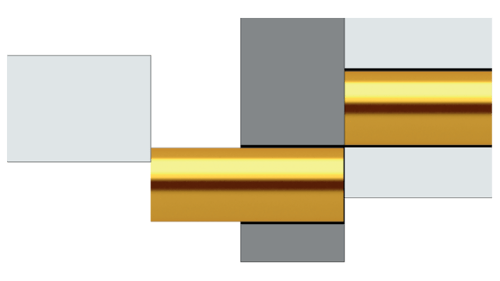
Coil wire is cut into billets of a predetermined length.
2. Forward Extrusion
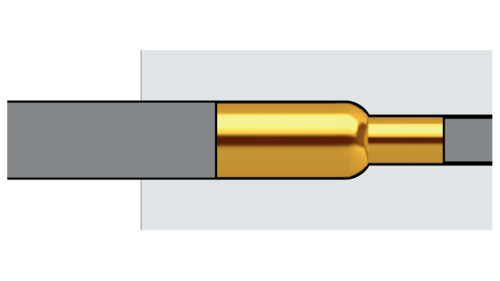
A processing method to reduce the diameter of a material by pushing it into a mold that is thinner than the material.
3. & 4. Upset
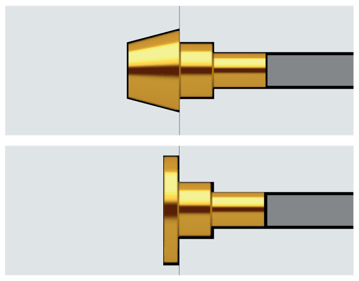
A processing method that utilizes perforated dies to facilitate material displacement. It is used to form shapes wider than the original material diameter.
5. Backward Extrusion
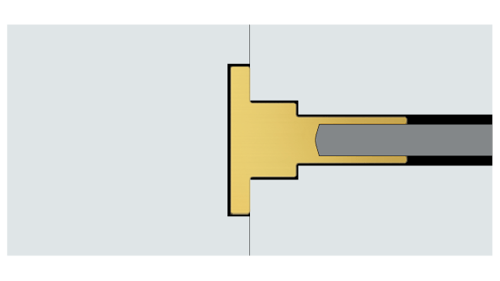
A processing method in which material is moved in the opposite direction of the force applied by the punch.
6. Processing Complete
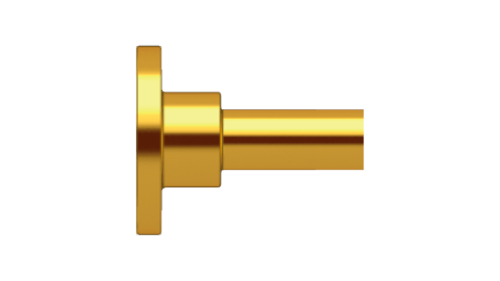
The completed part is ejected from the last die
4 Advantages of Cold Forming
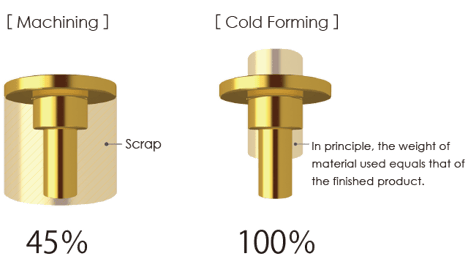
High efficiency material utilization (high yield)
The high material utilization of cold forging allows for significant reductions in material waste (scrap) compared to machining for the same geometry.
Figure: Material Yield Rate (multi-step rivet example)
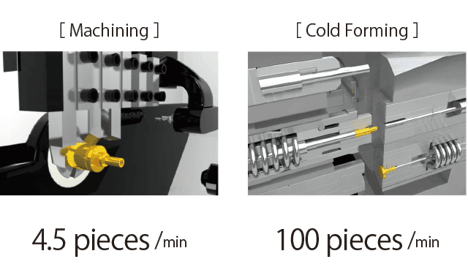
Higher speed, more efficient production
Cold forming allows for high speed manufacturing (around 100 parts/minute) while still maintaining high precision and complex product geometries. No heating of the material is required.
Figure: Production Speed (multi-step rivet example)
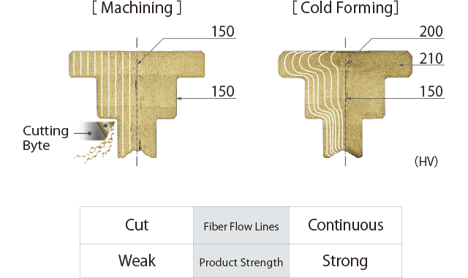
Improved product strength by work hardening
Cold forming process design takes fiber flow lines (the crystal structure of metals) into account allowing for stronger more durable parts.
Figure: Fiber Flow Lines (multi-step rivet example)
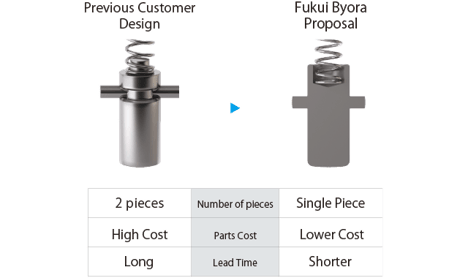
Cost reductions through customized manufacturing processes
If a customer design(tolerances, geometry, number of components required, etc) is practical using cold forming, significant improvements in part unit cost and reduced process complexity are possible.
Figure: Example of our Value Added / Value Engineering through cold forming
Materials Possible with Cold Forming
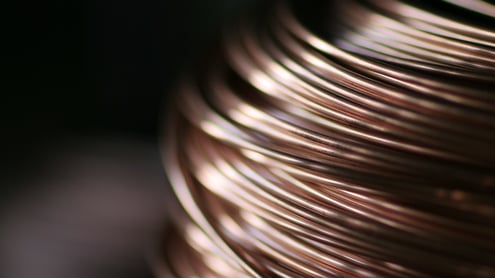
We have experience in processing the following materials with the cold forming process. If your preferred material is not listed below, please consult with us.
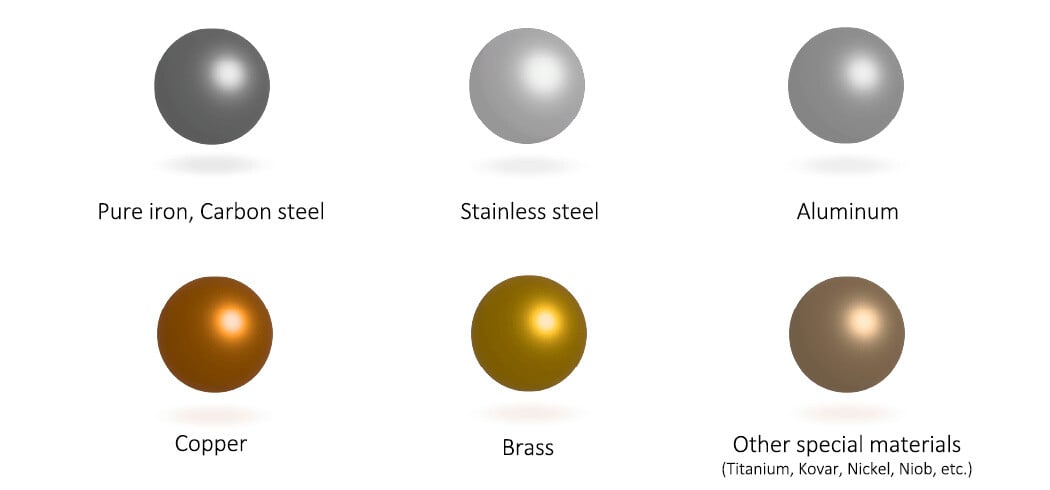
Processing Equipments
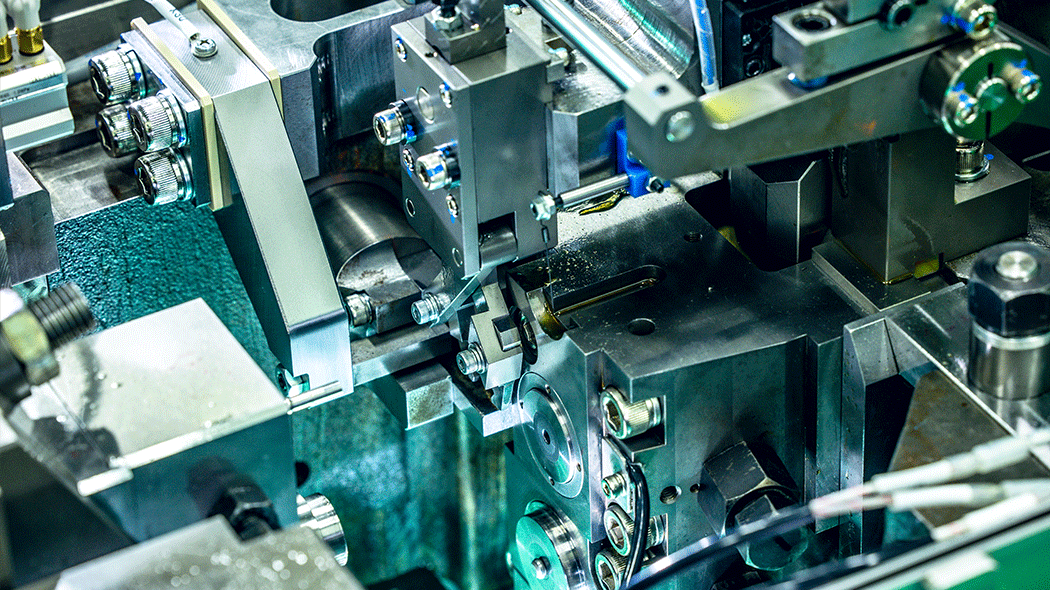
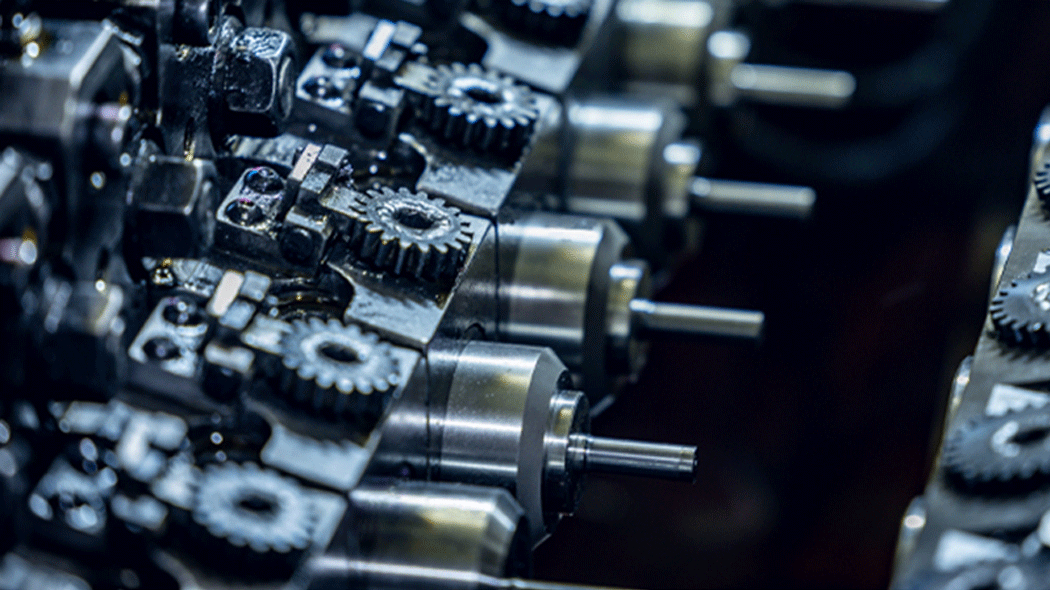
Range of Forming Machines |
1D2B~8D8B |
---|---|
Wire Diameter |
Φ 0.0039 in ~ Φ 0.9842 in |
Length |
0.0394 in ~ 47.24 in |
Control Precision |
µin (㎛) |